by Daniel Chin, Ian Zhang, and Gus Xia
Breath control 🤧🥱🥅
Breathing is becoming increasingly important for stress relief. However it is not only good for controlling the body, but also for controlling wind instruments for example the flute.
With the development of the Hyper hybrid flute, an attempt was made to integrate the profound role of breath control into a digital flute and to take it in advance it was successful. In principle, musicians can control not only the volume, but also articulation, octave, micro-tones, etc. through breathing techniques on wind instruments. However, most existing digital versions do not capture the various effects of breathing as is possible in analogue. Instead, they rely on additional interface elements. An interface was developed that converts real-time breath data into MIDI controls. The Hyper-hybrid Flute can be switched between its electronic and acoustic modes. In acoustic mode, the interface is identical to the regular six-hole recorder. In electronic mode, the interface recognizes the player’s fingering and breathing speed and converts them into MIDI commands.
SIDE NOTE: Definition of MIDI: MIDI stands for Musical Instrument Digital Interface, which means “digital interface for musical instruments”. It is a language that allows computers, musical instruments and other hardware to communicate with each other. The MIDI protocol includes the interface, the language in which the MIDI data is transmitted, and the connections needed for the hardware to communicate.
The Hyper-Hybrid Flute interface has three contributions in particular:
- It simulates that acoustic property of the flute where higher breathing speed leads to higher octaves and more micro-tonal pitch bending.
- By exaggerating the parameters, the interface is expanded into a hyper instrument.
- A simple toggle supports the change between electronic and acoustic mode.
To detect if the hole is covered by a finger when playing the flute, a ring-shaped capacitive sensor is placed on each of the six holes and the breathing rate is measured by a BMP085 air pressure sensor.
Changing state
To enter the electronic mode, the musician inserts the air pressure sensor into the mouthpiece outlet. This mutes the recorder and simultaneously exposes the sensor to the air pressure in the recorder, from which the breathing speed is calculated. To enter acoustic mode, the player releases the air pressure sensor from the exit port, so that the playing of the interface is acoustic and the air pressure sensor is not triggered. The picture below shows the prototype with the attached sensors.
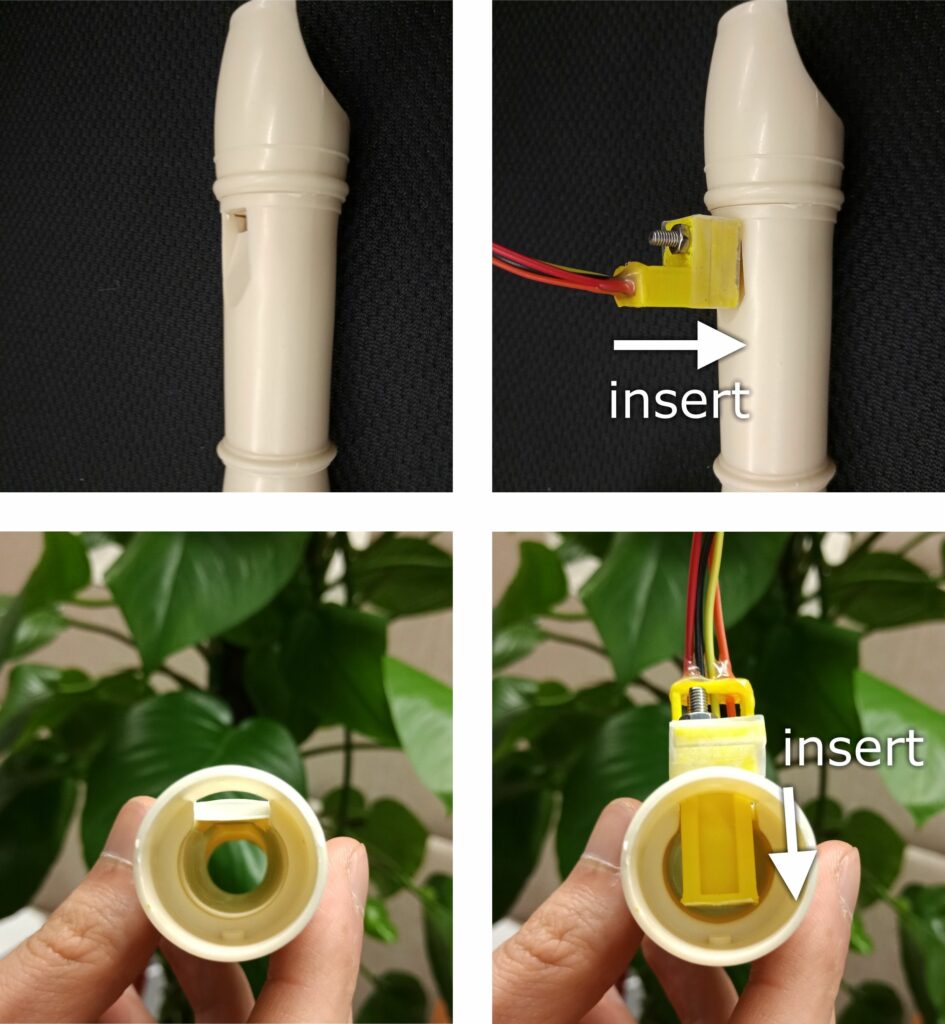
Controlling Octave and Micro-tone via Breath
The influence of the breath on the micro-tone and the octave can be modeled as follows:
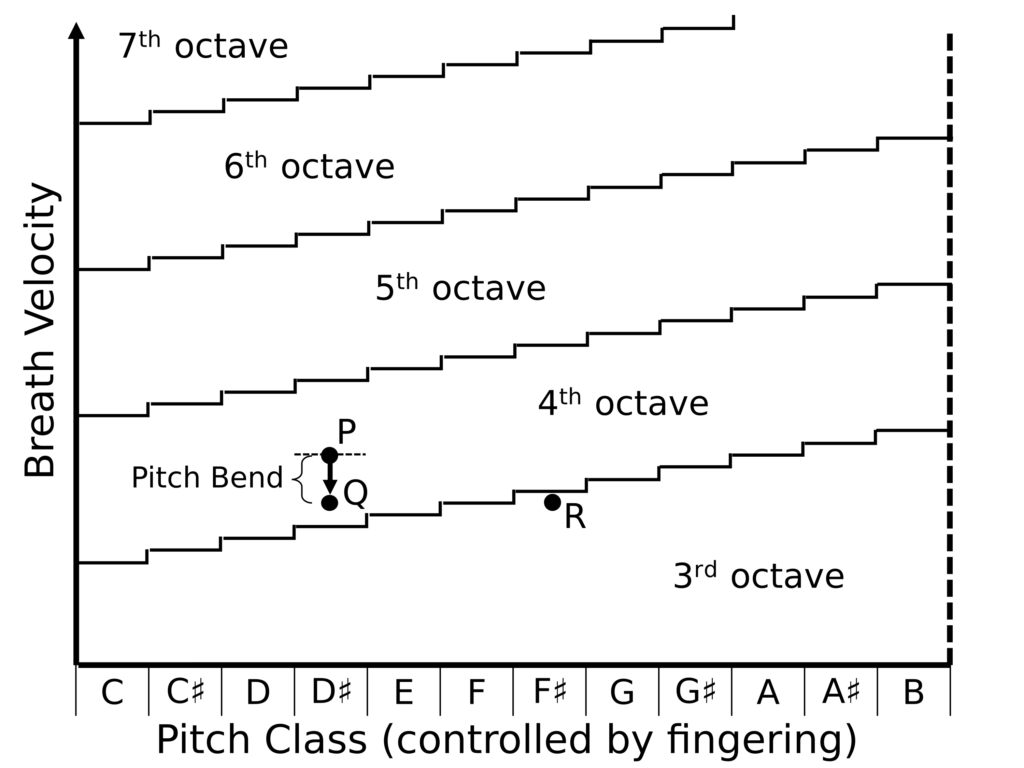
- Harder blowing at a pitch leads to an upward micro-tonal pitch bend.
- When the breathing speed exceeds a specific threshold, the pitch jumps up an octave.
Such threshold values for the breathing speed increase with rising pitch. This is shown perfectly in the picture above. The higher the velocity of the breath with holding for example D# the higher the jumps to another octave are.
Measuring the relationship between pitch bend and breath pressure using an acoustic recorder gives a pitch bend coefficient of 0.055. The micro-tone enables the musician to perceive his position relative to the thresholds. This interactive feedback allows them then to calibrate their breathing speed and avoid unexpected octave jumps. Under the bend coefficient > 0.055 the interface becomes a hyper instrument. The micro-tone as a musical device offers an additional dimension of expressiveness.
How does it become a MIDI controller?
To know what pitch the instrument should produce at any given time does not make it a MIDI controller per-se, because MIDI requires a discrete stream of note on and note off events. So the interface must be stateful.
The breath velocity is compared to a threshold to determine whether the instrument should be at rest or producing a note. A rising edge in that signal marks the excitation of the instrument, which fires a Note On event. Meanwhile, a differentiator listens to the pitch and fires its output line when the pitch changes value. The differentiator output, conditioned on whether the instrument is at rest, also fires a Note On event.
What tools are used?
The interface is wireless. All sensors are connected to an Arduino Nano, which communicates with a Processing 3 sketch via Bluetooth. The sketch uses the midi bus library for MIDI messaging. The recorder body is modeled in Fusion 360 and fabricated with MJF 3D printing.
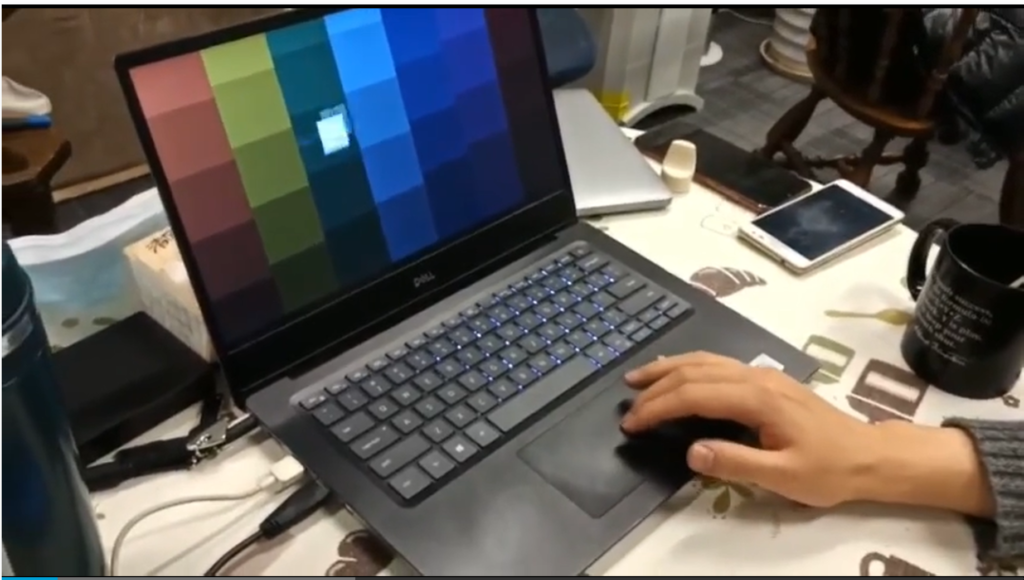
Reflections
In the results of this research, it is very clear that there is still innovation in the field of wind controllers. With the ability to measure octaves, the multi modal music teaching system can be expanded to include breathing technique in the learning outcomes. The MIDI interface is accurate and allows for optimal communication through the musician’s breathing.
Therefore, the hyper-hybrid flute poses as an interesting solution on the path to the digitization of wind instrument and also new didactic concept and learning more immersive. Besides teaching, I especially see this hyper-hybrid flute applied in the context of arts and performance art but also possible in commercial productions where simulations of wind instruments might be useful. Moreover I want to mention the importance of interfaces as bridges from the analogue to the digital world, what this flute also represents. It is of high interest to combine these worlds to create even better and more comprehensive solutions and experiences. Analog and digital, these opposites both have their justification and are to a certain extent equally dependent on each other, and definitely can profit from each others strengths.
I want to close this post with Adrian Belew’s words: “Digital for storage and quickness. Analog for fatness and warmth.”
Source: https://nime.pubpub.org/pub/eshr/release/1